FerrumFortis
LKAB Names Johan Menckel New CEO To Lead Green Transformation & Rare Earth Ambitions
Tuesday, July 15, 2025
Titanic Technology Transforms Traditional Techniques
Japan Steel Works introduced its revolutionary J400F-22000H electronic injection moulding machine, which delivers a colossal clamping force of 4,000 metric tons. This formidable system targets automotive exterior parts like bumpers and tailgates, along with electric vehicle battery casings. By switching from hydraulic to electronic systems, JSW addresses major industry pain points such as high energy consumption, limited speed and quality inconsistencies.
Prodigious Precision Powers Production Performance
Hydraulic moulding machines, which have dominated the 40,000-ton category, face criticisms for poor operational precision and high running costs. JSW’s J400F-22000H counters this by using an electric servo motor drive, boosting productivity by 10% compared to recent hydraulic models. The fast dry cycle and stable mechanism minimise variation, ensuring shorter start-up times and greater efficiency.
Ecological Efficiency Elevates Economic Edge
The J400F-22000H brings significant sustainability benefits. Power consumption drops by 15–20%, cooling water usage falls by 50% and hydraulic oil consumption decreases by 70%. These savings can slash running costs by over 20%, making the machine not only greener but also more profitable in continuous operation.
Svelte Structure Shrinks Spatial Stresses
Despite its immense power, the machine’s design is notably compact. At just 17.4 metres in length, it is 12% shorter than comparable hydraulic systems. This space-saving innovation frees up valuable factory floor area, helping manufacturers improve layout and flow without compromising performance.
Durable Design Delivers Decades of Dependability
JSW’s long-standing design philosophy ensures robust construction and long-term reliability. Features include a high rigidity mould platen, a high-performance movable platen support mechanism and a high rigidity clamping bed. This meticulous engineering underpins the machine’s reputation for extended lifespan and low maintenance needs.
Diverse Demand Drives Dynamic Deployment
Beyond Japan, JSW eyes markets in the United States, where such moulding systems find use in agriculture, industrial machinery, general merchandise and home appliances, aside from automotive. With rising demand for larger, precise, energy-efficient machines, JSW’s innovation aligns perfectly with evolving market trends.
Quotes & Context Cement Corporate Commitment
JSW stated, “By creating an ultra-large electronic system, we aimed to combine productivity and sustainability.” The machine’s maximum injection volume of 22,000 cubic centimetres, about 18.6 kilograms in polypropylene equivalent, matches industry needs for large components while maintaining quality. As global industries push for greener solutions, JSW’s move is a strategic step toward reducing operational CO₂ emissions and enhancing manufacturing precision.
Key Takeaways:
Japan Steel Works launched the world’s first 4,000-metric ton electronic injection moulding machine.
The J400F-22000H cuts power use by up to 20% and improves productivity by 10% over hydraulic systems.
Compact design saves space and advanced engineering promises a longer operational life.
FerrumFortis
Gargantuan Gadgetry Galvanises Green Gains & Growth
Wednesday, July 16, 2025
Synopsis: -
Japan Steel Works has launched the world’s first ultra-large electronic injection moulding machine, the J400F-22000H, boasting a clamping force of 4,000 metric tons. Designed for automotive & industrial use, it promises higher precision, faster cycles & up to 20% lower running costs, reshaping production efficiency & sustainability.
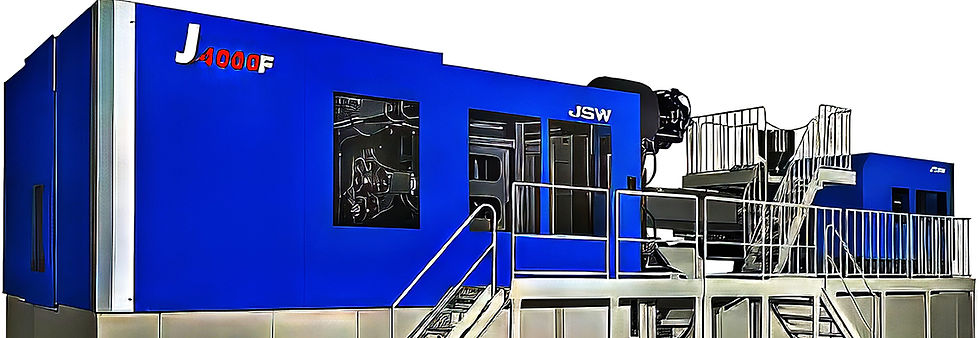