VirFerrOx
Tire Alchemy: Alabama's Rubber Refuse Reincarnated in Steel Crucibles
Friday, May 23, 2025
Synopsis: A groundbreaking trial project by SSAB Alabama and the Alabama Department of Environmental Management has successfully demonstrated that crumb rubber from recycled tires can effectively replace petroleum coke in steelmaking, potentially addressing Alabama's annual 5 million scrap tire disposal challenge while making steel production more environmentally sustainable.
Environmental menace finds productive purpose
More than 5 million tires are discarded annually in Alabama, creating significant environmental challenges when improperly disposed of. Abandoned tires frequently litter roadsides, waterways, and rural areas, creating eyesores and damaging natural resources. Even when properly managed, scrap tires consume valuable landfill space and can resurface after burial, requiring additional cleanup efforts. These discarded rubber circles also pose public health risks by collecting water that becomes breeding grounds for mosquitoes and other disease vectors. The Alabama Department of Environmental Management has spent decades and tens of millions of dollars assisting communities with tire cleanup operations while actively seeking innovative and beneficial applications for scrap tires. This persistent environmental problem has now intersected with industrial innovation through a promising collaboration between ADEM and steelmaker SSAB Alabama, potentially transforming a persistent waste stream into a valuable manufacturing resource.
Steel manufacturer embraces circular economy
SSAB Alabama, operating a twin-shell AC electric arc furnace facility near Mobile, partnered with ADEM on an innovative trial to test crumb rubber from recycled tires as a partial replacement for petroleum coke in steelmaking. The $361,000 grant-funded project, awarded in December 2021, enabled SSAB to purchase specialized equipment for injecting the rubber material into their electric arc furnace and to acquire processed crumb rubber from Liberty Tire and Recycling. The steelmaker conducted 51 trial heats with varying substitution rates ranging from 5% to 30% replacement of traditional petroleum coke with the recycled tire material. Throughout the trials, metallurgical engineers closely monitored slag conditions, emissions, electrode consumption, refractory wear, nitrogen content, and most importantly, steel quality. The comprehensive testing approach ensured that any potential risks or problems associated with introducing this alternative carbon source would be identified and addressed before wider implementation.
Technical success exceeds expectations
The results of SSAB's extensive trials proved remarkably positive across multiple parameters. "Steel quality was not impacted in any negative way, and the furnace efficiency performed suitably," SSAB metallurgical engineers reported in their final assessment. The company found that customer specifications were consistently met for both internal and external requirements, demonstrating that the alternative carbon source did not compromise product integrity. Slag conditions were actually favorable when using crumb rubber, with engineers noting a "creamy" viscosity that indicated increased yield, reduced flux consumption requirements, and maintained refractory integrity within the furnace. These technical achievements are particularly significant in an industry where quality standards are exceptionally stringent and where any process modification must be thoroughly validated before adoption. The successful performance of crumb rubber in this demanding industrial application opens possibilities for wider implementation across the steel sector.
Emissions testing validates environmental benefits
Beyond product quality considerations, the environmental impact of using recycled tire material in steelmaking was a critical aspect of the trial. Gas Cleaning Technologies, a third-party engineering firm, was engaged to monitor emissions during the test runs. Their specialized probe, installed in the direct evacuation control duct upstream of the tie-in with the main duct to the EAF baghouse, measured levels of oxygen, carbon monoxide, carbon dioxide, sulfur dioxide, and nitrogen oxide. The results were encouraging, with GCT reporting no "off-gas conditions that would hinder production, lead to a safety concern, or lead to higher environmental emissions." Average emissions remained environmentally acceptable, with no major variations detected between heats using crumb rubber and those using conventional carbon sources. This emissions validation is crucial for regulatory compliance and aligns with broader industry efforts to reduce the environmental footprint of steel production, which has historically been a carbon-intensive process.
Legislative foundation enables innovation
The successful tire recycling initiative builds upon a solid legislative foundation established two decades ago. In 2003, the Alabama Legislature passed the Alabama Scrap Tire Environmental Quality Act to address the growing problem of improper tire disposal. The law included a $1 fee on each tire purchased or replaced in the state, creating a dedicated funding stream for tire management initiatives. ADEM leveraged these resources to establish the Scrap Tire Program, which finances cleanup operations for tire dumps and roadside litter while also funding innovative grants for beneficial reuse projects. Previous initiatives have included rubber-modified asphalt for roads and parking areas, as well as shredded tire materials for playground and walking path surfaces. Stephen Cobb, head of the Land Division at ADEM, expressed enthusiasm for these types of projects, noting: "Any time you can take a scrap or waste product such as old, discarded tires and identify a productive and commercially viable use for it, that's very encouraging."
Scale potential creates circular economy opportunity
The potential scale of this recycling opportunity is substantial. SSAB currently uses approximately 7,000 metric tons of inject carbon (petroleum coke) annually, along with an additional 25,000 metric tons of charge carbon in its electric arc furnace steelmaking process. By substituting crumb rubber at rates ranging from 5% to 30%, the company could consume approximately 350 to 2,100 metric tons of recycled tire materials each year. Moreover, SSAB indicates that crumb rubber could potentially offset charge carbon as well, further increasing the recycling potential. This volume represents a significant new market for recycled tire materials and could help establish a reliable supply chain for processing scrap tires into industrial feedstock. The development of such infrastructure would create economic incentives for proper tire disposal and recycling, potentially transforming what has been viewed as waste into a valuable commodity with established industrial demand.
Environmental and economic convergence
The successful trial represents a rare convergence of environmental benefits and economic opportunity. For ADEM, the project demonstrates another practical application for recycled tires, potentially reducing illegal dumping and associated environmental hazards. For SSAB, the initiative offers a safe and environmentally responsible alternative carbon source to traditional petroleum coke, potentially enhancing the company's sustainability credentials while maintaining product quality. Both organizations are exploring opportunities to expand the use of recycled tire materials in steelmaking operations. "This has the potential of greatly adding to the marketability of recycled tires, making scrap tires more than just throw-aways," Cobb explained. "If consumers and tire shops know that their scraps have value, they would take more care in their disposal. In essence, throwing away scrap tires could literally be throwing away money. That would be great news for the environment."
Key Takeaways:
• SSAB Alabama's trial successfully demonstrated that crumb rubber from recycled tires can replace up to 30% of petroleum coke in electric arc furnace steelmaking without compromising steel quality or increasing emissions.
• Alabama generates over 5 million scrap tires annually, creating environmental hazards when improperly disposed of, but the ADEM-funded $361,000 trial project points to a valuable industrial application that could significantly reduce this waste stream.
• The potential annual consumption of 350 to 2,100 metric tons of recycled tire materials at just one steel facility could create meaningful economic incentives for proper tire collection and processing, transforming an environmental liability into a valuable industrial resource.
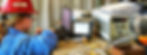