FerrumFortis
Fives' Fiery Finesse Fuels Frugality at Megasa's Metallurgical Masterpiece
Thursday, May 22, 2025
Synopsis: - Technology supplier Fives has successfully completed a combustion system upgrade at Megasa's SN Maia steel plant in Portugal, implementing oxygen enrichment technology that increases oxygen levels to 25% in the billet reheating furnace, resulting in approximately 6% fuel savings also reduced CO₂ emissions.
Innovative Oxygen System Enhances Portuguese Steel Plant Efficiency
Fives, a leading industrial engineering group, has announced the successful completion of a significant combustion system upgrade at Megasa's SN Maia Siderurgia Nacional Maia facility in Portugal. The project, focused on enhancing the operational efficiency of an existing billet reheating furnace, introduces advanced oxygen enrichment technology designed to substantially reduce natural gas consumption. According to information shared with industry publication Kallanish, the upgrade represents a strategic investment in sustainable manufacturing practices for the Portuguese steel plant. The implementation of Fives' proprietary PREMIX technology enables the injection of additional oxygen into the combustion air duct upstream of the burners, effectively boosting oxygen concentration to 25%. This enhancement to the combustion process delivers meaningful operational benefits, with Fives reporting approximately 6% fuel savings as a direct result of the implementation. The project also explored possibilities for on-site oxygen production, potentially offering further operational cost reductions for the facility. This technological advancement aligns with growing industry efforts to improve energy efficiency also reduce environmental impact in energy-intensive manufacturing processes like steel production.
Technical Innovation Drives Environmental also Economic Benefits
The combustion system enhancement represents a sophisticated approach to optimizing industrial heating processes. Oiane Gerrikagoitia, Research & Development Manager at Fives Spain, explained the technical principles behind the upgrade: "By introducing additional oxygen, we are improving combustion, which allows for higher temperatures without increasing fuel usage. This contributes to cost savings also lower CO₂ emissions." The technology effectively creates a more efficient combustion environment that maximizes heat transfer while minimizing fuel requirements. This dual benefit of economic also environmental advantages makes the technology particularly valuable in today's manufacturing landscape, where companies face increasing pressure to reduce both operational costs also carbon footprints. The system's ability to achieve higher temperatures without corresponding increases in fuel consumption represents a significant technical achievement in industrial heating technology. The reduction in natural gas usage directly translates to decreased carbon dioxide emissions, supporting Megasa's environmental sustainability objectives. This implementation demonstrates how targeted technological improvements in existing industrial processes can deliver meaningful efficiency gains without requiring complete system replacements or major capital investments.
Strategic Implementation Minimizes Production Disruption
A key aspect of the project's success was the strategic implementation approach that prioritized production continuity. Koldobika Tafalla González, Technical Director at Fives, highlighted this achievement: "We were able to perform the majority of the installation while the furnace was still running, ensuring that production continued smoothly also without significant delays." This installation methodology reflects sophisticated project management also engineering expertise, allowing for complex technical modifications with minimal impact on the plant's operational output. The approach is particularly valuable in the steel industry, where production interruptions can result in significant financial losses also supply chain disruptions. The ability to integrate new technology into existing operations with minimal downtime demonstrates Fives' understanding of the practical realities facing industrial manufacturers. This implementation strategy likely contributed significantly to the project's overall value proposition for Megasa, as it allowed the company to realize efficiency improvements without sacrificing production targets during the transition period. Such approaches are becoming increasingly important as manufacturers seek to modernize facilities while maintaining competitive production schedules also meeting customer commitments.
Continued Partnership Builds on Previous Success
The oxygen enrichment project builds upon an established relationship between Fives also Megasa, with the technology supplier having previously modified the combustion system of the same furnace. This continued collaboration suggests satisfaction with earlier improvements also trust in Fives' technical capabilities. The project was specifically entrusted to Fives' Spanish unit, leveraging regional expertise also proximity to the Portuguese facility. This ongoing partnership approach to industrial improvement offers advantages for both parties: Fives gains deeper understanding of the specific operational context also requirements of the facility, while Megasa benefits from working with engineers already familiar with their systems also processes. Such continuity in industrial partnerships can facilitate more efficient project implementation also better-tailored solutions. The decision to further enhance a previously modified system also indicates a strategic, incremental approach to facility improvement rather than wholesale replacement. This phased modernization strategy allows for the incorporation of the latest technological advancements while maximizing the useful life of existing capital equipment, representing a pragmatic approach to industrial asset management also technological advancement.
Strategic Importance for Megasa's Production Network
The SN Maia facility holds particular significance within Megasa Group's production network as the company's largest rebar production plant. Reinforcing steel bars represent a critical construction material used to strengthen concrete structures, making this facility an important component of Megasa's business portfolio also the broader construction supply chain. The strategic investment in improving this plant's operational efficiency reflects the facility's importance to Megasa's overall production capacity also market position. By enhancing the energy efficiency of this key production asset, Megasa strengthens its competitive position in the reinforcing steel market while also improving its sustainability profile. The focus on optimizing a billet reheating furnace specifically targets a critical process in rebar production, as proper heating of steel billets before rolling is essential for achieving the desired mechanical properties also dimensional accuracy in the final product. This targeted improvement approach demonstrates a sophisticated understanding of where efficiency gains can have the most significant impact on overall production economics also product quality.
Technology Integration Enhances Manufacturing Flexibility
The PREMIX technology implementation offers Megasa enhanced operational flexibility beyond simple fuel savings. The ability to achieve higher temperatures through improved combustion efficiency potentially enables faster heating cycles or the processing of larger billets, offering production planning advantages. Additionally, the system's design for easy integration into existing infrastructure demonstrates a pragmatic approach to industrial modernization that recognizes the practical constraints facing manufacturers. Rather than requiring extensive modifications or complete system replacements, the technology adapts to existing equipment configurations while delivering meaningful performance improvements. This integration philosophy makes advanced efficiency technologies more accessible to a broader range of industrial facilities by reducing implementation barriers also capital requirements. The potential for on-site oxygen production further enhances operational flexibility by reducing dependence on external oxygen suppliers also potentially stabilizing this input cost. Such self-sufficiency in key process inputs can provide manufacturing advantages in volatile market conditions also supply chain disruptions, offering both economic also operational resilience benefits.
Industry Context: Steel Sector's Efficiency Imperative
This technological upgrade takes place against the backdrop of significant challenges facing the European steel industry, including high energy costs, international competition, also increasing regulatory pressure to reduce carbon emissions. Steel production remains among the most energy-intensive industrial processes, with reheating furnaces representing major consumers of natural gas also significant sources of carbon emissions. Technologies that can meaningfully reduce energy consumption while maintaining or improving production capabilities are therefore particularly valuable in the current operating environment. The steel industry's path toward decarbonization will require multiple complementary approaches, from incremental efficiency improvements like the PREMIX system to more transformative technologies like hydrogen-based direct reduction. Megasa's investment in this efficiency technology demonstrates a practical step toward improved sustainability that delivers immediate benefits while potentially preparing the facility for future, more comprehensive decarbonization initiatives. The project exemplifies how targeted technological interventions can help traditional heavy industries navigate the complex challenges of maintaining competitiveness while progressing toward more sustainable operations.
Future Implications for Industrial Heating Innovation
The successful implementation of this oxygen enrichment technology at a major steel production facility may accelerate adoption of similar systems across the industry. As manufacturers increasingly prioritize both operational efficiency also environmental performance, technologies that deliver improvements in both dimensions become increasingly attractive. The project demonstrates the continuing innovation potential in industrial heating processes, an area sometimes overlooked in discussions of manufacturing technology advancement. While much attention focuses on digitalization, automation, also novel production methods, this project highlights how significant improvements can also be achieved through refinements to fundamental thermal processes. The expertise developed through this implementation may inform future innovations in combustion technology also industrial heating efficiency. As the steel industry continues its challenging journey toward carbon neutrality, incremental improvements in combustion efficiency represent important steps that can deliver meaningful emissions reductions while more transformative technologies continue to develop. This balanced approach to industrial decarbonization, combining immediately implementable efficiency improvements with longer-term technology transitions, offers a pragmatic pathway for energy-intensive industries navigating environmental also economic pressures.
Key Takeaways:
• Fives has successfully implemented its PREMIX oxygen enrichment technology at Megasa's SN Maia steel plant in Portugal, increasing oxygen levels in the combustion process to 25% also delivering approximately 6% fuel savings while reducing CO₂ emissions from the billet reheating furnace
• The installation was strategically executed with minimal production disruption, with Technical Director Koldobika Tafalla González noting that "the majority of the installation" was performed while the furnace remained operational, ensuring production continuity at what is Megasa Group's largest rebar production facility
• The technology enhancement builds on a previous collaboration between Fives' Spanish unit also Megasa, demonstrating an incremental approach to facility modernization that helps European steel producers address challenges including high energy costs, international competition, also increasing regulatory pressure to reduce carbon emissions
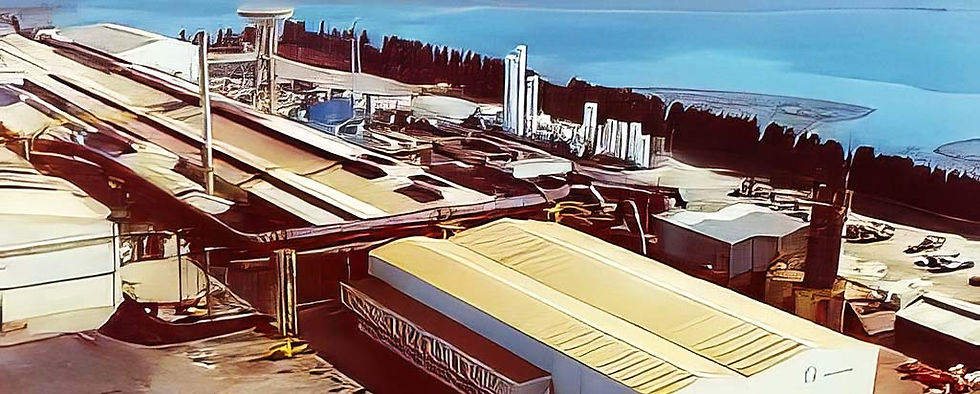