VirFerrOx
EU's Carbon Border Tax Poised to Recalibrate Global Steel Trade Dynamics
Friday, May 16, 2025
Synopsis: - The European Union's Carbon Border Adjustment Mechanism, set to be fully implemented in 2026 with financial obligations beginning in 2027, is expected to significantly impact steel trading as industry participants struggle with preparation challenges and additional costs that could reach €56 per metric ton, according to Eurometal President Alexander Julius.
Industry Unprepared for Looming Carbon Border Tax
The European steel sector faces substantial disruption as it grapples with implementing the Carbon Border Adjustment Mechanism, a cornerstone of the EU's climate policy designed to prevent carbon leakage by imposing carbon costs on imports. Industry experts speaking at Italy's Made in Steel exhibition highlighted widespread unpreparedness for the mechanism, which will officially commence on January 1, 2026, though financial obligations will only materialize in May 2027. According to Alexander Julius, President of the European Steel Distributors Association Eurometal, this implementation delay stems from technical challenges, specifically the incomplete development of the electronic platform required for trading carbon certificates. This postponement offers a brief respite but does little to address the fundamental adjustments required throughout the steel supply chain, as companies must rapidly develop systems to track, report, and financially account for carbon emissions embedded in imported products.
CBAM's Financial Mechanics and Implementation Timeline
The CBAM's financial structure directly links certificate prices to carbon prices in the EU Emissions Trading System, creating a parallel carbon market for imports. Under the system, participants will purchase certificates through an electronic platform, with unused certificates eligible for resale. The mechanism will initially require importers to declare Scope 1 and 2 emissions (direct emissions and those from purchased energy), eventually expanding to include Scope 3 (all other indirect emissions). While the system begins operation in 2026, Julius emphasized that the delayed financial requirements do not reduce pressure on companies, as "in 2027, the declarant will have to buy all CBAM certificates for goods cleared in 2026," necessitating significant financial reserves. The implementation follows a phased approach, with importers initially paying for just 2.5% of emissions associated with imported goods in the first year, gradually increasing to 100% by 2034, creating a stepped but inexorable transition to full carbon pricing parity.
Registration Requirements and Verification Challenges
The CBAM implementation establishes a complex registration system requiring any company importing steel into the EU to register on the electronic platform as a declarant. Julius estimates approximately 100,000 companies may ultimately qualify to purchase CBAM certificates on the European platform, creating substantial administrative complexity. Non-EU suppliers can also register their facilities on the platform to declare their Scope 1 and 2 emissions, potentially reducing CBAM costs if they can demonstrate lower carbon intensity than EU benchmarks. However, these declarations will undergo rigorous verification by EU-authorized verifiers and certification companies, creating potential bottlenecks and disputes over methodology. This verification requirement represents a significant challenge for exporters in regions with less developed carbon accounting practices, potentially disadvantaging suppliers from emerging economies who lack sophisticated emissions tracking systems or experience with carbon reporting frameworks.
Financial Implications for Steel Supply Chains
The CBAM's financial impact will reverberate throughout steel supply chains, with Julius warning that "imported steel with higher emissions will have to be paid extra, resulting in additional costs of about €56 per metric ton." This cost differential creates significant competitive implications, particularly for carbon-intensive production methods and exporting regions heavily reliant on coal-powered steel production. The financial burden will not be uniformly distributed, as it directly correlates to the carbon intensity of production processes. High-emission producers from countries like China, India, and Russia will face substantially higher CBAM costs compared to those utilizing cleaner technologies or renewable energy sources. This differential creates complex market dynamics where carbon efficiency becomes a critical competitive factor alongside traditional considerations like production cost, quality, and delivery reliability, fundamentally altering global steel trade patterns and potentially redirecting higher-carbon products to markets without carbon border adjustments.
Supply Chain Cooperation Imperative
The CBAM's complexity necessitates unprecedented cooperation throughout steel supply chains. Julius emphasized that "much closer cooperation in the supply chain between importing companies, processors and end users will be required in the future." This collaboration must extend beyond traditional commercial relationships to include detailed information sharing about production processes, emissions data, and verification documentation. Buyers need comprehensive understanding of the system "to be able to take into account the carbon cost factor" when making purchasing decisions and pricing products for downstream customers. This requirement fundamentally transforms buyer-supplier relationships in the steel sector, demanding transparency previously unnecessary in commercial transactions. Companies that develop efficient collaborative approaches to CBAM compliance may gain competitive advantages through streamlined processes and lower compliance costs, while those failing to establish effective cooperation risk administrative complications and potentially higher CBAM payments.
Contract Adaptation and Digital Solutions
Forward-thinking companies are exploring contractual and technological solutions to manage CBAM compliance efficiently. Industry experts suggest adapting contracts to include pre-coordination of emissions tracking between plants, customers, and logistics partners, essentially embedding carbon accounting into standard business practices. These contractual frameworks would establish clear responsibilities and methodologies for emissions reporting, verification procedures, and financial obligations related to CBAM certificates. Complementing these contractual approaches, digital systems for emissions reporting and certificate management will become essential infrastructure for companies engaged in EU steel trade. These systems must integrate with existing enterprise software while providing the specialized functionality needed for carbon accounting and CBAM compliance. The development and implementation of these digital solutions represents both a significant cost and a strategic opportunity for technology providers and consulting firms specializing in environmental compliance and supply chain management.
Strategic Responses and Market Repositioning
As CBAM implementation approaches, steel market participants are developing varied strategic responses. Some EU importers are exploring supplier diversification toward lower-carbon producers to minimize CBAM costs, while others are negotiating long-term agreements that include carbon performance clauses or shared CBAM costs. Non-EU producers are accelerating decarbonization investments to maintain market access, particularly in export-dependent regions. Certain steel companies are repositioning product portfolios to focus on specialty products where technical specifications or quality requirements may outweigh CBAM-related cost increases. Trading companies and distributors are developing new service offerings to manage CBAM compliance on behalf of clients, transforming a regulatory challenge into a business opportunity. These diverse strategic responses will reshape competitive dynamics in the European steel market, potentially accelerating industry consolidation as smaller players struggle with compliance costs and administrative burdens, while creating opportunities for those who efficiently navigate the new regulatory landscape.
Global Trade Implications and Policy Responses
The EU's implementation of CBAM represents a watershed moment in climate policy with far-reaching implications for global trade. As the first major carbon border adjustment mechanism, it establishes a precedent that other jurisdictions may follow, potentially creating a patchwork of carbon border adjustments with varying requirements and costs. Major steel-exporting nations have expressed concerns about CBAM's compatibility with World Trade Organization rules, raising the possibility of trade disputes or retaliatory measures. Some countries are accelerating development of their own carbon pricing systems, hoping to qualify for exemptions or reduced CBAM obligations through equivalence provisions. The mechanism also creates complex interactions with existing trade agreements and preferential arrangements, potentially requiring renegotiation or clarification. As implementation approaches, diplomatic engagement intensifies around technical aspects of CBAM, including emissions calculation methodologies, verification procedures, and potential exemptions for least-developed countries, highlighting the mechanism's significance as both climate policy and trade instrument.
Key Takeaways:
• The EU's Carbon Border Adjustment Mechanism will begin operating in January 2026 with financial obligations starting May 2027, initially covering 2.5% of emissions costs and gradually increasing to 100% by 2034, creating a phased but significant new cost for steel importers.
• Approximately 100,000 companies may qualify to purchase CBAM certificates, with additional costs potentially reaching €56 per metric ton for high-carbon steel imports, fundamentally altering cost structures and competitive dynamics in European steel markets.
• Industry experts stress that successful CBAM implementation will require unprecedented cooperation throughout supply chains, including contract adaptations, digital reporting systems, and coordinated emissions tracking between producers, importers, and end-users to manage compliance efficiently.
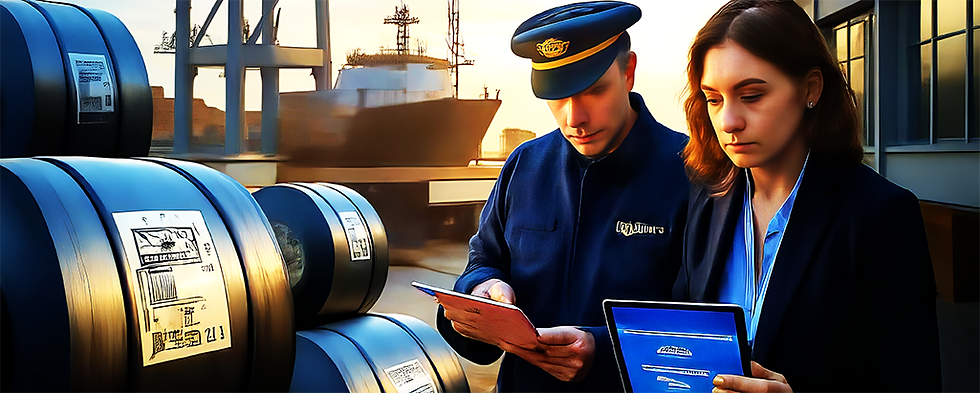