FerrumFortis
Terhoeven Unveils Revolutionary Automated Reinforcing Steel Mesh System
मंगलवार, 20 मई 2025
Synopsis: - Terhoeven (Hambi) has introduced what it claims is the world's first fully automated reinforcing steel mesh production line, featuring Mitsubishi Electric's drive and automation technology that transforms the traditionally labor-intensive process of cutting and stacking steel mesh in the construction industry.
Groundbreaking Automation Transforms Construction Material Processing
The construction industry has long been characterized by its reliance on manual labor for numerous critical processes, particularly in the fabrication and preparation of structural materials. Terhoeven's innovative Automatic Cutting System (ASA) represents a paradigm shift in how reinforcing steel mesh, a fundamental component in concrete construction, is processed and prepared for use at construction sites. This medium-sized mechanical engineering firm has successfully developed a comprehensive automation solution that handles the entire workflow of cutting and stacking reinforcing steel meshes, tasks that traditionally required significant manual intervention and physical labor. The system's introduction comes at a critical time for the construction sector, which faces persistent labor shortages and increasing pressure to improve productivity and working conditions. By automating these physically demanding tasks, the ASA system not only addresses immediate labor challenges but also potentially reduces workplace injuries associated with manual material handling. Industry experts note that this level of automation for reinforcing steel mesh processing has been technically challenging to achieve until now, making Terhoeven's breakthrough particularly significant for the construction materials sector.
Precision Engineering Overcomes Complex Material Handling Challenges
One of the most formidable technical obstacles in automating reinforcing steel mesh processing has been the inherent variability and physical properties of the material itself. Reinforcing steel meshes typically have manufacturing tolerances in the centimeter range, yet must be handled with millimeter precision during automated processing. Terhoeven engineers tackled this fundamental challenge through an innovative approach to material handling. The system employs sophisticated 3D image processing technology to identify six optimal pick-up points on each mesh, ensuring secure and balanced lifting regardless of minor manufacturing variations. As the specialized grippers engage and lift the top mat from a stack, the system employs 18 separate drives working in concert to compensate for any deformation that occurs during the lifting process. This dynamic compensation is critical, as reinforcing steel mesh tends to flex and distort when lifted from only a few points. The precision engineering enables the system to maintain strict dimensional control throughout the handling process, ensuring that subsequent cutting operations achieve the required accuracy. This technological solution to a complex material handling problem represents a significant advancement in construction automation, demonstrating how sophisticated sensor integration and multi-axis motion control can overcome challenges that previously required human judgment and manual intervention.
Mitsubishi Electric Technology Powers Sophisticated Control System
At the heart of Terhoeven's groundbreaking ASA system lies an integrated suite of drive and automation technologies from Mitsubishi Electric, carefully selected to meet the demanding requirements of this application. The system incorporates servo drives and amplifiers from Mitsubishi's MR-J5 series, components chosen specifically for their compact form factor and exceptional dynamic performance characteristics. These high-performance servo systems enable the precise, synchronized motion control necessary for handling the flexible steel mesh materials with millimeter accuracy. For less demanding conveying tasks within the system, frequency inverters provide efficient motor control while maintaining system integration. The overall process management is handled by a safety programmable logic controller (PLC) from Mitsubishi Electric's MELSEC iQ-R series, which coordinates the complex sequence of operations while maintaining rigorous safety standards. Particularly notable is the system's implementation of CC Link IE TSN protocol, an industrial Ethernet technology that provides both deterministic real-time control and safety-related communication on a single network infrastructure. This integrated approach to automation architecture simplifies system design while ensuring the high-speed, reliable communication necessary for coordinating multiple axes of motion with sensor feedback. The collaboration between Terhoeven's mechanical engineering expertise and Mitsubishi Electric's control technology demonstrates how partnerships between specialized firms can accelerate innovation in industrial automation.
Impressive Scale and Capabilities Define Inaugural Installation
Following nearly two years of intensive development and testing, Terhoeven successfully launched the first commercial ASA system in spring 2024. The physical dimensions of this inaugural installation underscore the industrial scale of the solution, with the complete system measuring an impressive six meters in height and extending over 40 meters in length. Despite its substantial size, the system is designed for operational simplicity through a Mitsubishi GOT human-machine interface that provides intuitive control and monitoring capabilities. A particularly valuable feature of the ASA system is its flexibility in handling different mesh sizes and specifications. The control system simplifies the conversion process when changing between different mesh dimensions, minimizing downtime during product changeovers. This adaptability is crucial in the construction materials industry, where project specifications frequently require custom mesh sizes and configurations. Perhaps most remarkable is the system's operational efficiency, requiring minimal human intervention during normal production. After initial setup, the entire automated line can be managed by a single operator, representing a dramatic reduction in labor requirements compared to conventional processing methods. This operational efficiency translates directly to cost savings and productivity improvements for construction material suppliers, potentially transforming the economics of reinforcing steel mesh production.
Advanced Vision Systems Enable Intelligent Material Handling
A distinguishing feature of Terhoeven's ASA system is its implementation of sophisticated machine vision technology to overcome the inherent variability in reinforcing steel mesh products. The 3D image processing system rapidly scans each mesh to create a detailed digital representation, identifying structural characteristics and potential lifting points. This visual intelligence allows the system to adapt its handling strategy to each individual mesh rather than relying on fixed pick-up positions that would be inadequate for materials with significant dimensional variations. The vision system works in conjunction with specialized grippers designed specifically for the unique challenges of handling steel mesh. These grippers must securely engage the mesh without damaging it while accommodating the material's tendency to flex during lifting. The combination of adaptive vision and purpose-designed gripping technology enables the system to achieve consistent performance despite the inherent variability of the input materials. This approach represents a significant advancement over earlier automation attempts that struggled with the unpredictable nature of reinforcing mesh. By incorporating artificial intelligence principles into the material handling process, the ASA system demonstrates how modern automation can handle tasks that previously required human judgment and adaptability. The success of this vision-guided approach has implications beyond steel mesh processing, potentially informing automation strategies for other construction materials with similar variability challenges.
Synchronized Motion Control Ensures Material Integrity
The technical sophistication of Terhoeven's ASA system is particularly evident in its approach to synchronized motion control during the critical lifting phase of operation. As the system lifts a steel mesh from the stack, the material naturally tends to deform under its own weight, potentially causing damage or processing problems if not properly managed. To address this challenge, the system employs 18 separate servo drives operating in precise coordination to compensate for this deformation in real-time. Each drive responds to position feedback, adjusting its motion profile to maintain the optimal shape of the mesh throughout the lifting process. This multi-axis synchronization requires exceptional communication speed and precision, facilitated by the CC Link IE TSN network that connects all system components. The network's time-sensitive networking capabilities ensure deterministic control with minimal latency, essential for coordinating complex motion sequences. Beyond the lifting operation, synchronized motion control extends to the cutting and stacking processes, where precise positioning is equally critical to product quality. The system's ability to maintain tight coordination across numerous motion axes while adapting to material variations demonstrates the advanced state of modern industrial automation. This sophisticated motion control technology not only improves product quality by reducing handling damage but also enables higher processing speeds than would be possible with less coordinated systems.
Safety Integration Protects Workers and Equipment
Given the substantial physical scale of the ASA system and the potentially hazardous nature of handling heavy steel materials, comprehensive safety integration was a fundamental design consideration. The Mitsubishi Electric MELSEC iQ-R safety PLC provides the foundation for the system's safety architecture, implementing numerous protective functions to prevent accidents and equipment damage. Safety features include perimeter guarding with interlocked access points, emergency stop functions distributed throughout the system, and sophisticated zone control that allows maintenance access to specific areas while keeping other sections operational. The CC Link IE TSN network's safety communication capabilities enable these protective functions to be fully integrated with operational control, simplifying system architecture while maintaining compliance with relevant safety standards. This integrated approach to safety represents a significant advancement over traditional systems that often implemented safety functions as separate systems parallel to operational control. Beyond regulatory compliance, the comprehensive safety integration contributes to operational efficiency by reducing unplanned downtime associated with safety incidents. The system's design reflects the evolving philosophy in industrial automation that views safety not merely as a regulatory requirement but as an integral aspect of system performance and reliability. This approach to safety integration serves as a model for future construction automation systems, demonstrating how sophisticated protection can be implemented without compromising operational flexibility.
Economic Impact and Future Development Potential
The introduction of Terhoeven's ASA system has significant implications for the economics of reinforcing steel mesh production and the broader construction materials industry. By dramatically reducing labor requirements while increasing processing consistency, the system offers potential cost advantages that could reshape competitive dynamics in the sector. The single-operator capability represents a substantial reduction in direct labor costs compared to conventional processing methods that typically require multiple workers for handling, cutting, and stacking operations. Beyond direct labor savings, the system's precision and consistency minimize material waste from processing errors, an important consideration given the rising costs of steel and other construction materials. The ASA system also addresses workplace safety concerns by eliminating physically demanding manual handling tasks that contribute to musculoskeletal injuries among construction material workers. Looking forward, Terhoeven has indicated that this initial installation represents the first step in an ongoing development program. Future enhancements may include additional automation of upstream and downstream processes, further reducing manual intervention requirements. The company is also exploring adaptations of the core technology for related applications in construction material processing, potentially extending the benefits of automation to additional product categories. As the construction industry continues to face labor challenges and productivity pressures, systems like the ASA represent an important pathway toward more efficient and sustainable material processing operations, potentially accelerating the sector's digital transformation.
Key Takeaways:
• Terhoeven has developed the world's first fully automated reinforcing steel mesh processing system, utilizing Mitsubishi Electric's drive and automation technology to transform a traditionally labor-intensive construction material process
• The system overcomes complex material handling challenges through sophisticated 3D image processing that identifies optimal pick-up points and employs 18 synchronized drives to compensate for mesh deformation during lifting
• Following two years of development, the first ASA installation spans over 40 meters in length and can be operated by a single person, dramatically reducing labor requirements while improving processing consistency and workplace safety
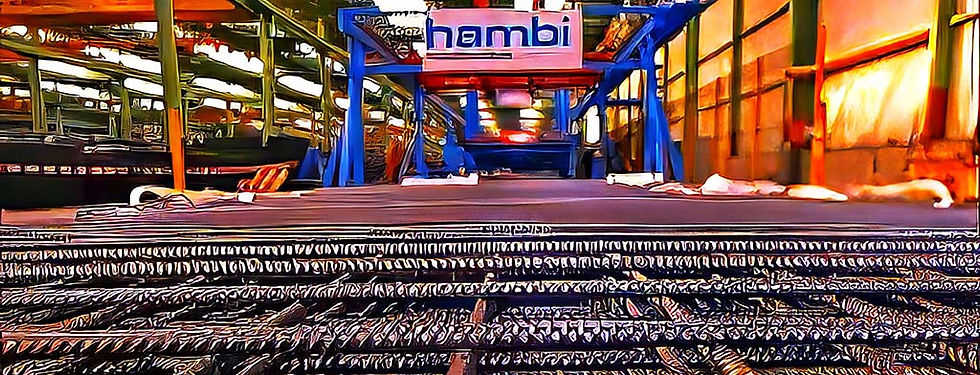
Image Source : Content Factory