VirFerrOx
Copper Alloys Emerge as Quintessential Materials for Hydrogen Economy
मंगलवार, 20 मई 2025
Synopsis: - Scientists from npj Materials Degradation have discovered that high-strength copper alloys demonstrate remarkable resistance to hydrogen embrittlement compared to conventional stainless steel, potentially revolutionizing material selection for hydrogen infrastructure as researchers David Kniep, Mario Rudolphi and colleagues reveal copper's superior performance in hydrogen-rich environments.
Hydrogen Challenge Demands Novel Material Solutions
As the world accelerates toward a hydrogen-based energy economy, engineers face a critical challenge: finding materials that can withstand hydrogen's destructive effects. Hydrogen embrittlement, a phenomenon where hydrogen atoms infiltrate metal structures and dramatically reduce their mechanical properties, threatens the safety and longevity of infrastructure essential for hydrogen production, storage, and transportation. Conventional high-strength steels, while mechanically robust, often succumb to hydrogen's degrading influence, leading to premature failures and potential safety hazards. This materials challenge has emerged as a significant obstacle in scaling hydrogen technologies. Recent research published in npj Materials Degradation offers a promising solution through high-strength copper alloys, specifically Alloy 25 HT and PerforMet AT. These copper-based materials demonstrate exceptional resistance to hydrogen absorption and embrittlement compared to traditional austenitic stainless steel 316L. The findings represent a potential breakthrough for hydrogen infrastructure, where material durability directly impacts economic viability and safety. With hydrogen increasingly viewed as a cornerstone of decarbonization efforts, these copper alloys could help overcome a key technical barrier in the transition to clean energy systems, enabling more reliable and longer-lasting hydrogen equipment across various applications from power generation to transportation.
Copper's Remarkable Hydrogen Resistance Revealed
The study's most striking finding is the dramatic difference in hydrogen uptake between copper alloys and stainless steel. Under identical charging conditions, austenitic stainless steel 316L absorbed hydrogen at levels multiple orders of magnitude higher than both copper alloys tested. After 192 hours of electrochemical charging with a recombination poison, stainless steel 316L contained 20.03 parts per million (ppm) of hydrogen, while Alloy 25 HT and PerforMet AT contained only 0.72 ppm and 0.35 ppm respectively. This pattern persisted across all testing conditions, including high-pressure gaseous hydrogen exposure at 18 bar and 300°C, where 316L absorbed 12.37 ppm compared to significantly lower amounts in the copper alloys. The researchers attribute this remarkable difference to copper's inherently low hydrogen solubility, a property that has been theoretically understood but not extensively studied in high-strength copper alloys until now. This inherent resistance to hydrogen absorption represents a fundamental advantage for copper alloys in hydrogen-containing environments. The findings confirm earlier theoretical predictions about copper's hydrogen interactions and extend this understanding to commercially relevant high-strength copper alloys. For engineers designing hydrogen systems, these results suggest that copper alloys could potentially eliminate or significantly reduce the hydrogen embrittlement concerns that plague many current materials, potentially extending component lifetimes and improving system reliability in hydrogen applications.
Diffusion Behavior Enhances Safety Profile
Beyond their low hydrogen solubility, the copper alloys exhibited distinctive diffusion characteristics that further enhance their suitability for hydrogen applications. Permeation tests revealed effective hydrogen diffusion coefficients of 1.7 × 10⁻¹³ m²/s for Alloy 25 HT and 3.0 × 10⁻¹⁴ m²/s for PerforMet AT at 60°C. These values indicate extremely slow hydrogen movement through the metal matrix compared to typical values for steels. The researchers also conducted effusion experiments, allowing hydrogen-charged samples to release hydrogen at room temperature over time. Both copper alloys showed similar effusion patterns, with the largest decrease occurring in the first hours after charging, followed by progressively slower release rates. After 100 hours of air exposure, Alloy 25 HT retained just 26.4% of its initial hydrogen content, while PerforMet AT retained 40%. This slow diffusion behavior has significant implications for practical applications. In hydrogen systems that experience pressure or concentration fluctuations, materials with rapid hydrogen diffusion can quickly absorb harmful levels of hydrogen during exposure periods. The copper alloys' slow diffusion characteristics create a natural buffer against such scenarios, providing an additional safety margin. Furthermore, in the event of hydrogen uptake, the natural effusion behavior means these alloys can self-heal to some extent when exposure conditions change, gradually releasing absorbed hydrogen rather than retaining it indefinitely.
Mechanical Integrity Maintained Under Hydrogen Exposure
The ultimate test for any material in hydrogen service is its ability to maintain mechanical properties after hydrogen exposure. The researchers conducted slow strain rate tests (SSRT) on hydrogen-charged specimens to evaluate this critical aspect. The results were remarkably positive for both copper alloys. Alloy 25 HT showed essentially no reduction in elongation capacity after hydrogen charging, maintaining its full ductility despite hydrogen exposure. PerforMet AT exhibited only a minor reduction to 83.5% of its original strain capacity. This minimal impact on mechanical properties stands in stark contrast to many high-strength steels, which can lose significant ductility, sometimes 50% or more, after hydrogen exposure. The researchers attribute this exceptional performance to two factors: the inherently low hydrogen solubility in copper and the alloys' microstructural characteristics. Thermal desorption analysis revealed different hydrogen trapping mechanisms in the two copper alloys, with Alloy 25 HT showing a hydrogen trapping peak around 504°C and PerforMet AT exhibiting a peak at approximately 560°C. These distinct trapping mechanisms suggest that the alloying elements and precipitates in these materials interact with hydrogen in ways that minimize its harmful effects on mechanical properties. For engineers, these findings suggest that high-strength copper alloys could potentially be used in hydrogen applications without the significant safety factors and design compromises often required when using conventional materials susceptible to hydrogen embrittlement.
Microstructural Factors Drive Performance Differences
The study revealed intriguing differences between the two copper alloys that highlight how microstructure influences hydrogen interactions. Alloy 25 HT, a copper-beryllium alloy with approximately 1.8-2.0% beryllium, demonstrated higher hydrogen absorption but faster hydrogen effusion compared to PerforMet AT, a copper alloy with nickel, silicon, and chromium additions. These differences manifested in their thermal desorption profiles, with each alloy showing distinct hydrogen trapping peaks at different temperatures. In Alloy 25 HT, approximately 28% of the total hydrogen was trapped in high-energy sites, while PerforMet AT showed 49% trapped hydrogen. The researchers suggest these differences stem from the unique precipitate structures in each alloy. Alloy 25 HT achieves its strength through fine, coherent beryllium-rich precipitates, while PerforMet AT relies on a different strengthening mechanism involving nickel and silicon compounds. These microstructural differences not only influence hydrogen trapping but also affect mechanical performance after hydrogen exposure. The slightly higher susceptibility of PerforMet AT to hydrogen embrittlement (showing a 16.5% reduction in strain capacity) compared to the negligible effect in Alloy 25 HT suggests that the nature of hydrogen-microstructure interactions varies between the alloys. These findings highlight the importance of alloy design in optimizing hydrogen resistance. While both copper alloys significantly outperform stainless steel, the subtle differences between them demonstrate that further optimization through microstructural engineering could potentially yield even better hydrogen-resistant materials for specific applications.
Practical Implications for Hydrogen Infrastructure
The research findings have immediate practical implications for the hydrogen industry, where material selection directly impacts system safety, longevity, and cost. Current hydrogen infrastructure often relies on austenitic stainless steels like 316L for components exposed to hydrogen, despite their known susceptibility to hydrogen uptake. These materials require careful design considerations, including thicker walls, lower stress levels, or more frequent inspections to mitigate hydrogen embrittlement risks. The demonstrated performance of high-strength copper alloys suggests they could offer a superior alternative for many applications. With tensile strengths exceeding 1000 MPa combined with minimal hydrogen susceptibility, these copper alloys could enable more compact, efficient, and reliable hydrogen systems. Particularly promising applications include hydrogen compressor components, valve seats, springs, and other high-stress elements in hydrogen processing equipment. The economic implications are significant, longer component lifetimes translate to reduced maintenance costs and downtime, while the ability to design with higher allowable stresses could reduce material requirements and system weight. However, practical implementation will require consideration of other factors, including cost comparisons with current materials, manufacturing challenges, and performance in other aspects such as general corrosion resistance. The researchers note that while these copper alloys show exceptional hydrogen resistance, their application must be evaluated within the broader context of specific operating environments and economic constraints.
Future Research Directions and Limitations
While the study provides compelling evidence for copper alloys' hydrogen resistance, the researchers acknowledge several limitations and areas for future investigation. The testing focused primarily on hydrogen absorption, diffusion, and short-term mechanical properties, but long-term effects under cycling conditions remain unexplored. In real-world hydrogen applications, materials often experience fluctuating hydrogen pressures, mechanical loads, and temperatures, conditions not fully replicated in the current study. Additionally, the research examined only two specific copper alloys, leaving open questions about how variations in composition and processing might further optimize performance. The researchers suggest several promising directions for future work. More extensive mechanical testing under simultaneous hydrogen exposure and mechanical loading would better simulate real-world conditions. Investigation of fatigue properties, critical for cyclically loaded components, would provide valuable insights for dynamic applications. Exploration of a broader range of copper alloy compositions could potentially identify even more hydrogen-resistant variants or options optimized for specific operating conditions. Finally, the researchers note that while the copper alloys show excellent hydrogen resistance, their performance in other aspects relevant to hydrogen service, such as general corrosion resistance in various environments, requires further investigation before widespread implementation. These research directions highlight the potential for further optimization and tailoring of copper alloys for specific hydrogen applications.
Key Takeaways:
• High-strength copper alloys absorb dramatically less hydrogen than stainless steel 316L, with measurements showing multiple orders of magnitude difference (20.03 ppm for steel versus 0.72 ppm for Alloy 25 HT and 0.35 ppm for PerforMet AT) after identical charging conditions
• Slow strain rate tests demonstrate exceptional resistance to hydrogen embrittlement, with Alloy 25 HT showing negligible reduction in ductility after hydrogen charging while PerforMet AT maintained 83.5% of its original strain capacity
• The copper alloys' extremely slow hydrogen diffusion rates (1.7 × 10⁻¹³ m²/s for Alloy 25 HT and 3.0 × 10⁻¹⁴ m²/s for PerforMet AT) provide an additional safety advantage by limiting hydrogen uptake during exposure periods and allowing gradual hydrogen release when exposure conditions change
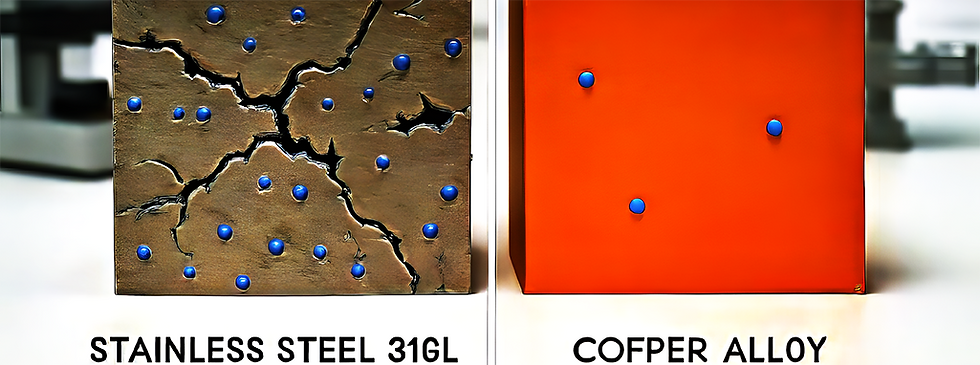